Pressure Testing Equipment
FST has led the design, construction, and overall solutions for multiple national-level high-temperature and high-pressure laboratories, representing the technological high ground for domestic high-temperature and high-pressure laboratory construction.
The Gas Testing unit uses high-pressure nitrogen to perform sealing tests on specimens, in order to meet the requirements of manufacturers and testing agencies for sealing tests on valves, wellhead Christmas trees, blowout preventers, and manifold.
For the gas tightness test of valves and wellhead Christmas trees, a multi-stage pneumatic booster pump is used for pressurization. The test meets the requirements of standard API Spec 6A and the specifications of PSL1-PSL4. p>
For the gas test of blowout preventers and manifold, a hydraulic-driven booster pump is used, which has high efficiency and large displacement. The test meets the requirements of standard API 16A. p>
Hydrostatic Pressure Testing Unit
The sealing performance of the test piece is tested with high-pressure purified water to meet the requirements of manufacturers and testing organizations for water pressure testing of valves, wellhead Christmas trees, BOP, and manifold.
For the Hydrostatic pressure testing of valves and wellhead Christmas trees, a multi-stage pneumatic booster pump is used for pressurization. It complies with the American API 6A testing standard and the specifications of PSL1-PSL4. p>
For the Hydrostatic pressure testing of BOP and manifold, a hyraudlic-driven booster pump is used, which has high efficiency and large displacement. The test meets the requirements of standard API 16A. p>
According to the different needs of customers, we have selections of pressure sources with different pressure levels and automation levels, which are widely used in various skid mounted testing vehicles and containerized portable pressure testing equipment.
Application objects/scenarios: Various skid mounted testing vehicles and containerized pressure testing equipment. p>
The PR2 system consists of a high and low temperature environmental chamber, valve driving device (torque testing tool), water/gas pressurizing equipment, measuring and control system, and monitoring system. It can automatically conduct test for the pressure, temperature, and torque combined cycle tests specified by the PR2 standard. It meets the requirements of standards such as API 6A, ISO 10423, GB 10592.
Application objects/scenarios: The strength and sealing test of ram BOP, annular BOP, valve, hanger, Christmas tree and other wellhead products, the dynamic test of valve opening and closing at maximum/minimum temperatures, valve pressure/temperature cycling tests, torque tests, etc. p>
p>
The BOP Testing System consists of the following components: p>
The BOP pressure testing unit: is used in conjuction with other systems to perform pressure fatigue test, hydrostatic test, ram closing test, tripping test. Also conduct the tests for hangers, packers,shears, seals, and control units. p>
The BOP leak testing unit: pressurizes the test target, and observes the pressure decline. it opens or closes the device by controlling different output circuits. p>
The seals temperature testing unit: verifies the performance of non metallic seals used as pressure-controlling and/or pressure containing during the exposure to low and high temperatures. p>
The data collection and monitoring system: monitors and controls the entire testing process and achieve fully automation control.
p>
11D1 HPHT Validation Test System
The 11D1 HPHT Validation Test System mainly consists of a high-pressure/ultra-high-pressure testing well for downhole tools, an intelligent high-pressure/ultra-high-pressure oil, gas, and water boosting system, a force loading testing device, a circulation heating and insulation device, and a remote central measurement and control system.
Application objects/scenarios:
It is mainly used to simulate the high-temperature and high-pressure environment of downhole tools such as packers and bridge plugs in actual working conditions. According to API 11D1 standard, V0 level verification tests are carried out, including gas tests, axial load tests, temperature cycle tests, and zero gas bubble acceptance standards for performance testing of packers and bridge plugs. It includes envelope curve verification tests for downhole tools, as well as pressure and temperature resistance tests for other instruments and tools that require high-temperature and high-pressure environment testing. At the same time, it provides testing means for the development of new downhole tools. p>

Shenzhen Fluid Science&Technology Corp., Ltd.
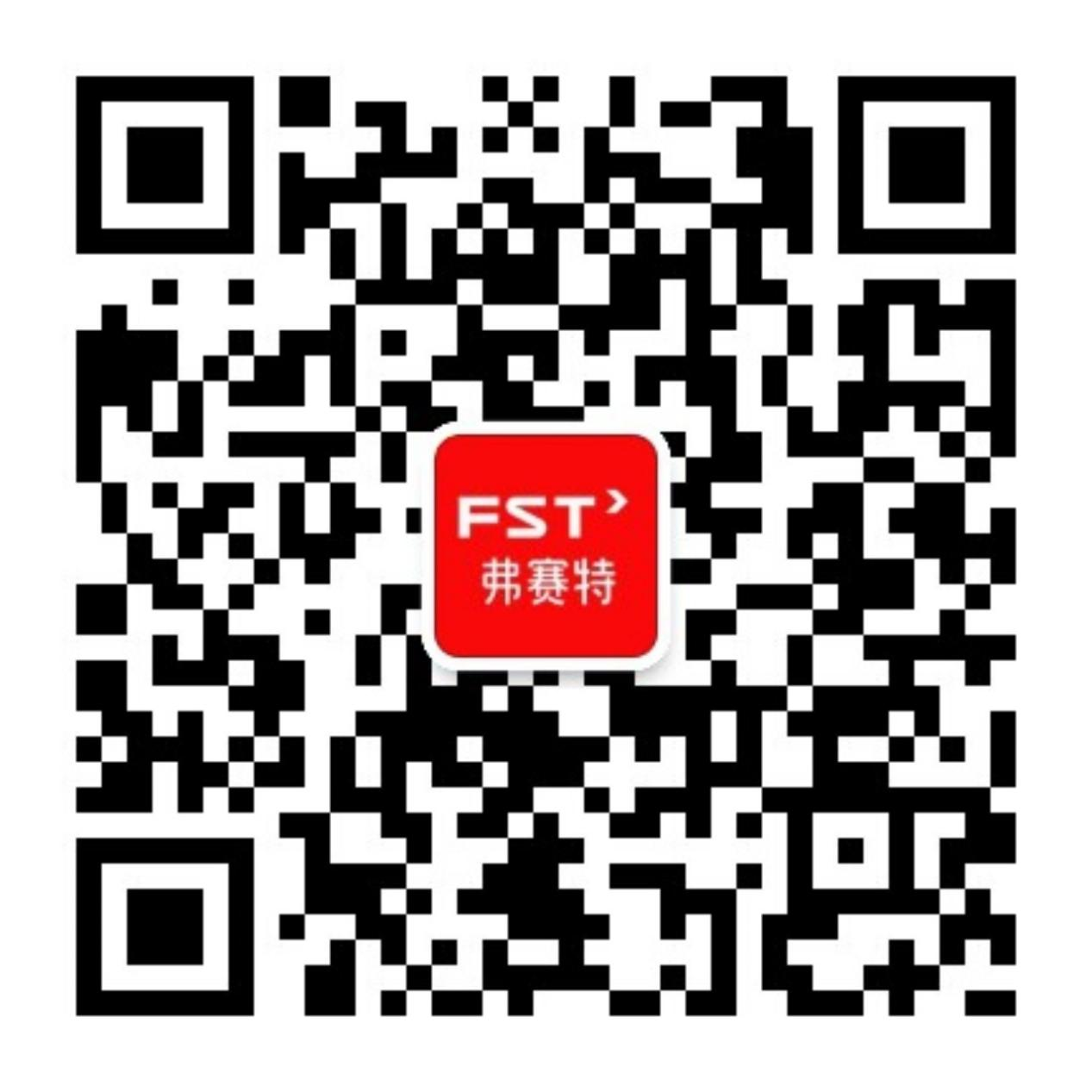
Headquarter:
Room 904, Block B, Building 10, Shenzhen Bay Science and Technology Ecological Park, No.10 Gaoxin South 9th Road, Nanshan District, Shenzhen, 518063 Guangdong, P.R China.
Tel:
© Shenzhen Fluid Science&Technology Corp., Ltd. ALL RIGHTS RESERVED | 粤ICP备10233873号 | Legal Declaration